Precision Plastic Molding: Revolutionizing Manufacturing
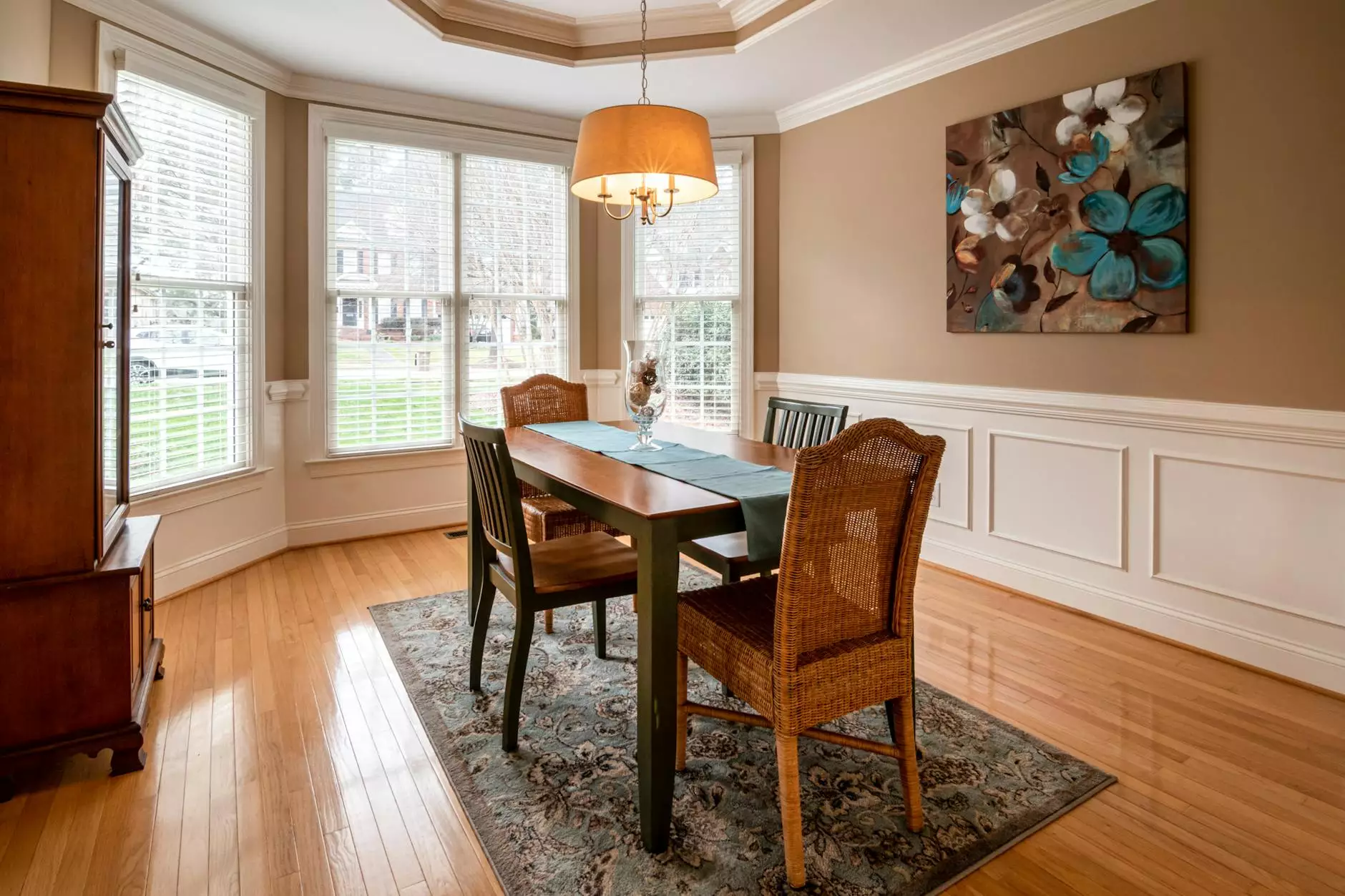
In the ever-evolving landscape of manufacturing, precision plastic molding has emerged as a cornerstone technique that enhances efficiency, quality, and innovation across multiple industries. With rising demand for precision-engineered components, understanding this method's role becomes paramount for businesses, especially within the category of metal fabricators.
What is Precision Plastic Molding?
Precision plastic molding is an advanced manufacturing process where molten plastic is injected into a precisely engineered mold cavity, allowing for the replication of intricate shapes and designs. This method is renowned for its ability to produce high-volume parts with consistent quality, earning it a revered position in various sectors, including automotive, electronics, medical, and consumer goods.
The Evolution of Plastic Molding Technologies
Historically, plastic molding originated in the early 20th century but has significantly evolved through technological advancements. Innovations such as computer-aided design (CAD) and computer numerical control (CNC) machining have transformed traditional practices, enabling unparalleled accuracy and efficiency.
Types of Precision Plastic Molding
There are several widely used types of precision plastic molding, each tailored for specific applications:
- Injection Molding: The most common form, injecting molten plastic into a mold.
- Blow Molding: Used for creating hollow plastic parts by inflating heated plastic within a mold.
- Rotational Molding: A process that rotates a mold to create hollow items with uniform wall thickness.
- Compression Molding: Involves pressing material into a mold and applying heat and pressure to achieve the desired shape.
The Benefits of Precision Plastic Molding
The adoption of precision plastic molding presents numerous advantages that enhance both product quality and production efficiency:
1. High Precision and Consistency
This method allows for high tolerances, ensuring that each part is manufactured to exact specifications. Consistency in quality reduces waste and saves costs, making it a preferred choice in industries requiring extreme accuracy.
2. Cost-Effectiveness
After the initial setup and tooling, the cost per unit is significantly reduced in mass production scenarios. This economic advantage makes precision plastic molding a feasible option for high-volume manufacturing.
3. Design Flexibility
Designers can create complex geometries that would be unattainable using traditional methods. As a result, precision plastic molding facilitates innovation, enabling companies to bring new products to market rapidly.
4. Material Variety
A wide selection of plastics can be molded, including thermoplastics, thermosetting plastics, and elastomers. This versatility allows manufacturers to select materials that best suit their product needs, optimizing performance and durability.
Applications of Precision Plastic Molding
Precision plastic molding serves a multitude of sectors, reflecting its adaptability and efficiency:
1. Automotive Industry
In automotive manufacturing, precision plastic components play critical roles in interior and exterior assemblies, ensuring weight reduction while maintaining structural integrity.
2. Electronics Manufacturing
The electronics sector relies on precision plastic molding for creating intricate components such as enclosures, connectors, and casings that protect sensitive circuitry.
3. Medical Devices
The demand for precise, sterile, and reliable medical device components has led to the increased use of plastic molding in producing instrument housings and single-use products.
4. Consumer Goods
From kitchen utensils to toys, precision plastic molding offers manufacturers the ability to create aesthetically pleasing, functional, and ergonomic products.
The Manufacturing Process: From Concept to Completion
The journey from design to finished product in precision plastic molding involves several critical phases:
1. Design and Prototyping
Using advanced CAD software, designers create detailed 3D models of products, which are crucial for visualizing how the finished item will look and function. Prototyping allows for revisions before mass production, saving time and money.
2. Mold Creation
Once the design is finalized, precision molds are crafted using CNC machines. The mold quality directly impacts the final product’s precision, durability, and clarity.
3. Injection and Cooling
The heating process melts the plastic, which is then injected into the mold. After cooling, the part is ejected, completing the initial production stage.
4. Quality Assurance and Finishing
Every component undergoes rigorous quality checks. Additional processes such as painting, printing, or assembling may follow to complete the product.
Challenges in Precision Plastic Molding
Despite its many benefits, precision plastic molding does encounter challenges that companies must navigate:
1. Upfront Costs
The initial investment in mold design and machinery can be substantial, which may deter smaller businesses.
2. Material Limitations
Not all plastics are suitable for molding, and variations in material properties can affect the quality of the final product.
3. Tooling and Setup Time
Creating highly detailed molds can be time-consuming, leading to longer lead times before production begins.
Staying Competitive: Best Practices for Metal Fabricators
For metal fabricators embracing precision plastic molding, implementing the following strategies can enhance competitiveness:
- Invest in Advanced Technologies: Utilize the latest manufacturing technologies to improve precision and efficiency.
- Prioritize Quality Control: Establish comprehensive quality assurance protocols to ensure consistency and reliability.
- Explore R&D Opportunities: Collaborate with research institutions to innovate new materials and processes.
- Focus on Sustainability: Adopt eco-friendly materials and processes to meet growing consumer demand for sustainable products.
Conclusion
Precision plastic molding stands as a transformative force within the manufacturing landscape, especially valuable to metal fabricators looking to innovate and optimize their production capabilities. As industries continue to advance, investigating and adopting this method will ensure companies remain at the forefront of manufacturing excellence. The future of manufacturing is bright, and those who leverage precision plastic molding will undoubtedly lead the way.