The Future of Plastics Molding: Innovations and Applications
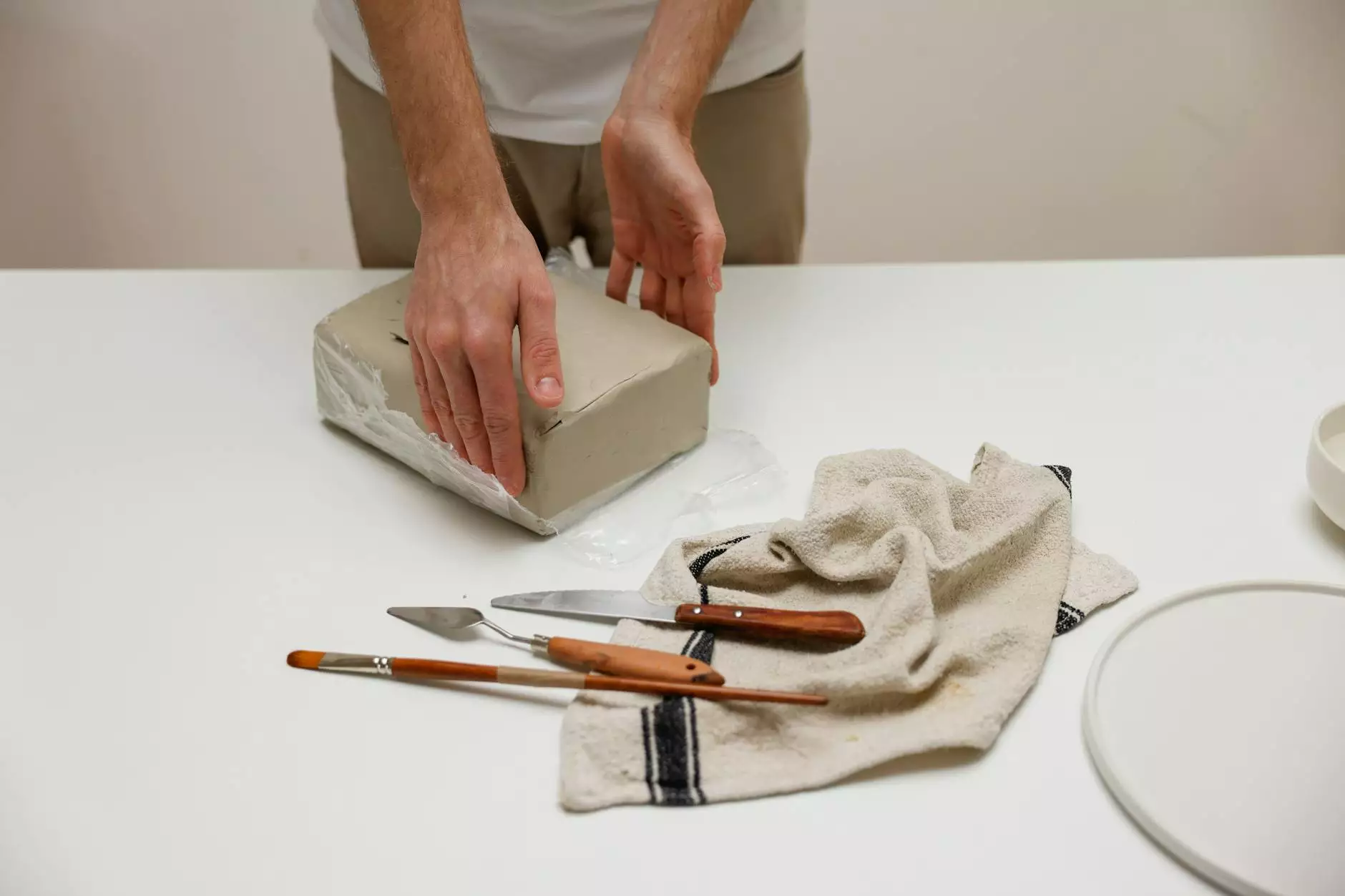
In the contemporary landscape of manufacturing, plastics molding has emerged as a cornerstone process that drives innovation across multiple industries. As businesses strive for efficiency and cost-effectiveness, the role of plastics molding has become increasingly pivotal. This article delves into the intricacies of plastics molding, exploring its various techniques, applications, and the latest advancements that promise to redefine manufacturing in the coming years.
Understanding Plastics Molding
Plastics molding is a manufacturing process that involves shaping plastic materials into desired final products. The process can be adapted to create a vast range of items—from automotive parts to household goods, and everything in between. The precision and adaptability of plastics molding make it an essential technique in the production line of countless goods.
The Core Processes of Plastics Molding
The primary plastics molding processes include:
- Injection Molding: This involves injecting molten plastic into a mold, where it cools and hardens into the final shape. This method is renowned for its ability to produce complex geometries with high precision.
- Blow Molding: Used primarily for producing hollow objects, blow molding entails inflating hot plastic into a mold. This method is commonly used for manufacturing containers and bottles.
- Rotational Molding: In this process, plastic is heated and rotated within a mold to produce hollow items. It is particularly effective for large, hollow products.
- Thermoforming: This method involves heating a plastic sheet until it becomes pliable, then forming it over a mold. It is often used for packaging materials and trays.
The Importance of Plastics Molding in Modern Manufacturing
As global manufacturing trends evolve, the importance of plastics molding cannot be overstated. Its versatility and efficiency offer several advantages:
- Cost-efficiency: With rapid production speeds and low waste rates, plastics molding reduces overall manufacturing costs.
- Design Flexibility: The nature of plastics allows for intricate designs that would be impossible through other manufacturing means.
- Material Versatility: A wide range of plastic materials can be utilized to cater to specific performance requirements, enhancing product functionality.
- Automation Compatibility: Most plastics molding processes can be automated, leading to increased production rates and consistency.
Applications of Plastics Molding Across Industries
The applications of plastics molding span numerous sectors, illustrating its versatility:
Automotive Industry
In the automotive sector, plastics molding is crucial for producing lightweight yet durable components. This not only lowers vehicle weight, enhancing fuel efficiency, but also enables the integration of complex designs that contribute to vehicle aesthetics and functionality.
Consumer Goods
From kitchen utensils to electronic casing, consumer goods rely heavily on plastics molding for mass production. The ability to create visually appealing and ergonomically designed products at scale is a significant advantage for manufacturers.
Medical Devices
The medical field utilizes plastics molding for a variety of applications, including surgical tools and packaging solutions. The ability to maintain strict hygienic standards is paramount, and advanced molding technologies allow for seamless manufacturing that complies with medical regulations.
Latest Innovations in Plastics Molding
The landscape of plastics molding is continuously evolving with technological advancements:
3D Printing Integration
3D printing technology is increasingly being integrated with traditional plastics molding processes. This fusion allows for rapid prototyping and customized production runs, enhancing design capabilities while maintaining cost efficiency.
Biodegradable Plastics
With rising environmental concerns, the development of biodegradable plastics has gained momentum. Manufacturers are now exploring plastics molding techniques using eco-friendly materials that do not compromise on performance while contributing to sustainability efforts.
Smart Molding Technology
This includes the use of IoT (Internet of Things) technology to monitor and optimize the molding process in real-time. Such innovations enhance operational efficiency and reduce downtime, ultimately leading to reduced costs and improved product quality.
Challenges Facing the Plastics Molding Industry
Despite its advantages, the plastics molding industry faces several challenges:
- Environmental Regulations: Stricter regulations regarding plastic use and disposal are putting pressure on manufacturers to adapt.
- Material Costs: Fluctuating costs of raw materials can impact production budgets and profitability.
- Technological Adaptation: Keeping up with rapid technological changes can be a significant challenge, especially for smaller manufacturers.
Looking Ahead: The Future of Plastics Molding
The future of plastics molding appears bright, given the continued demand for plastic products across various industries and the ongoing advancements in technology. Key trends likely to shape its future include:
- Sustainability Initiatives: A shift towards sustainable practices, including increased use of recycled materials and greener manufacturing processes.
- Advanced Robotics: Greater incorporation of robotics in the molding process to enhance precision and efficiency.
- Customization: Growing demand for custom solutions will lead to the increased use of flexible and adaptive manufacturing techniques.
Conclusion
In conclusion, plastics molding is a dynamic and essential process that plays a significant role in modern manufacturing. Its versatility, efficiency, and adaptability to new technologies position it as a key player in the future of various industries. Staying abreast of the latest trends and challenges will allow manufacturers to leverage the full potential of plastics molding, ultimately driving growth and innovation in their respective markets.
For more insights into plastics molding and its potential applications in your business, visit DeepMould.net.